Understanding Electric Moulding Machines: Revolutionizing Metal Fabrication
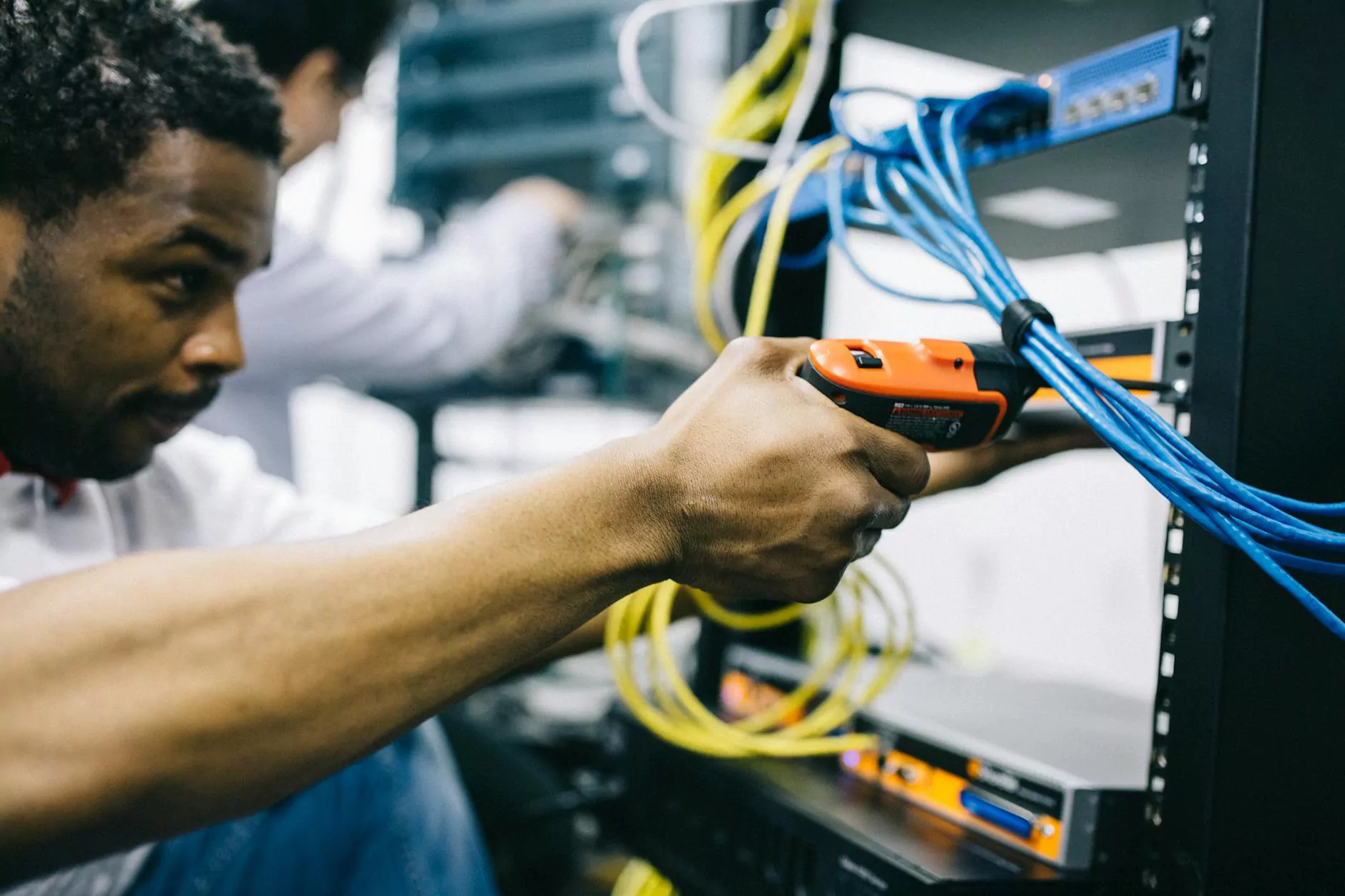
The realm of metal fabrication is continuously evolving, with innovations designed to increase productivity, efficiency, and accuracy. Among these advancements, the electric moulding machine has emerged as a revolutionary tool that is transforming production environments. This article delves into the world of electric moulding machines, examining their importance in the manufacturing process, their benefits, and their role in modern metal fabrication.
What is an Electric Moulding Machine?
An electric moulding machine is a tool used for shaping metal materials into desired forms. Unlike traditional hydraulic moulding machines, which utilize hydraulic fluid pressure, electric moulding machines leverage electric motors to drive their operations. This transition from hydraulic to electric systems has opened up various advantages for manufacturers.
How Electric Moulding Machines Operate
Electric moulding machines function by converting electrical energy into mechanical energy. Here's a general overview of their operational process:
- Power Supply: The machine is powered through an electrical connection that provides energy to the motor.
- Motor Activation: The electric motor drives the screws and other components, translating rotational motion into linear motion.
- Moulding Process: Raw materials are fed into the machine, where they are heated and then forced into the mould under pressure.
- Cooling and Solidification: The material cools and solidifies to take the shape of the mould.
- Finishing: Once cooled, the formed metal part is released from the mould and undergoes any necessary finishing processes.
The Advantages of Electric Moulding Machines
The shift to electric moulding machines has ushered in a range of benefits for manufacturers. Let’s explore some key advantages:
1. Enhanced Precision
Electric moulding machines are known for their high precision in producing detailed parts. This level of accuracy minimizes waste and ensures a high-quality product, crucial for industries where tolerances are tight.
2. Improved Energy Efficiency
Electric machines consume less power compared to their hydraulic counterparts. This energy efficiency leads to lower operating costs and contributes positively to a company’s sustainability goals.
3. Faster Cycle Times
Thanks to their rapid cycle speeds, electric moulding machines can achieve more cycles per hour compared to traditional machines. This capability results in increased productivity, allowing manufacturers to meet tight deadlines and higher demand.
4. Reduced Maintenance Requirements
Electric moulding machines have fewer moving parts than hydraulic machines, leading to reduced wear and tear. As a result, maintenance needs decrease, allowing manufacturers to save on repair costs and downtime.
5. Consistent Output Quality
With advanced control systems, electric moulding machines provide consistent and reliable results, ensuring that each batch meets the same high-quality standards as the previous one.
Applications of Electric Moulding Machines in Metal Fabrication
Electric moulding machines find applications across various sectors, particularly in metal fabrication. Let’s discuss a few of the industries where they are essential:
1. Automotive Industry
In the automotive sector, precision and quality are paramount. Electric moulding machines enable manufacturers to create intricate components such as gears, housings, and brackets that require meticulous attention to detail.
2. Aerospace Industry
The aerospace industry relies heavily on electric moulding machines for manufacturing lightweight yet durable components. The precision of these machines supports the rigorous standards necessary for aircraft parts.
3. Electronics Manufacturing
With the increase in demand for electronic devices, electric moulding machines have become crucial in creating metal enclosures and components that house delicate electronic systems.
4. Construction Industry
The construction industry uses electric moulding machines for producing various metal fixtures, brackets, and fittings, which require rigorous durability and strength.
Choosing the Right Electric Moulding Machine
Selecting the perfect electric moulding machine for your needs involves considering several critical factors:
1. Production Volume
Assessing your production volume is essential. Machines designed for high volumes may differ significantly from those intended for smaller batches.
2. Material Type
Different machines cater to various materials, including metals like aluminum, steel, or alloys. Ensure your chosen machine can handle your material requirements.
3. Mold Design and Complexity
Consider the designs you will be moulding. Complex geometries may require more advanced machines capable of intricate operations.
4. Manufacturing Space
The size and layout of your manufacturing facility will also influence your choice. Ensure you select a machine that fits seamlessly into your workspace without disrupting your operations.
The Future of Electric Moulding Machines
The future prospects for electric moulding machines are bright, with continuous advancements in technology promising even greater efficiency and functionality. Here are a few trends to watch:
1. Automation and Smart Technologies
As industries embrace Industry 4.0, we can expect electric moulding machines to integrate more complex automation features, including AI and IoT capabilities. This will facilitate real-time monitoring and predictive maintenance, enhancing operational efficiency.
2. Sustainability Initiatives
With sustainability becoming a significant focus for manufacturers, electric moulding machines will likely evolve to use more environmentally friendly materials and processes. This shift will align with global efforts to reduce carbon footprints across industries.
3. Enhanced User Interfaces
Future machines will likely come with advanced user interfaces that enhance operator control and experience. These interfaces will simplify the setup, monitoring, and adjustment processes, making it easier for technicians to operate the machines proficiently.
Conclusion
In summary, the electric moulding machine represents a critical advancement in the field of metal fabrication, reshaping how manufacturers approach production in a competitive market. With their numerous advantages, including enhanced precision, reduced operating costs, and faster cycle times, electric machines are set to play a vital role in the manufacturing processes of various industries. As the future unfolds, these machines will continue to improve, integrating smart technologies and promoting sustainability—making them indispensable tools for modern metal fabrication.
For more information about electric moulding machines and how they can benefit your manufacturing processes, visit deepmould.net today!