Understanding Precision Machining CNC: A Key Player in Modern Metal Fabrication
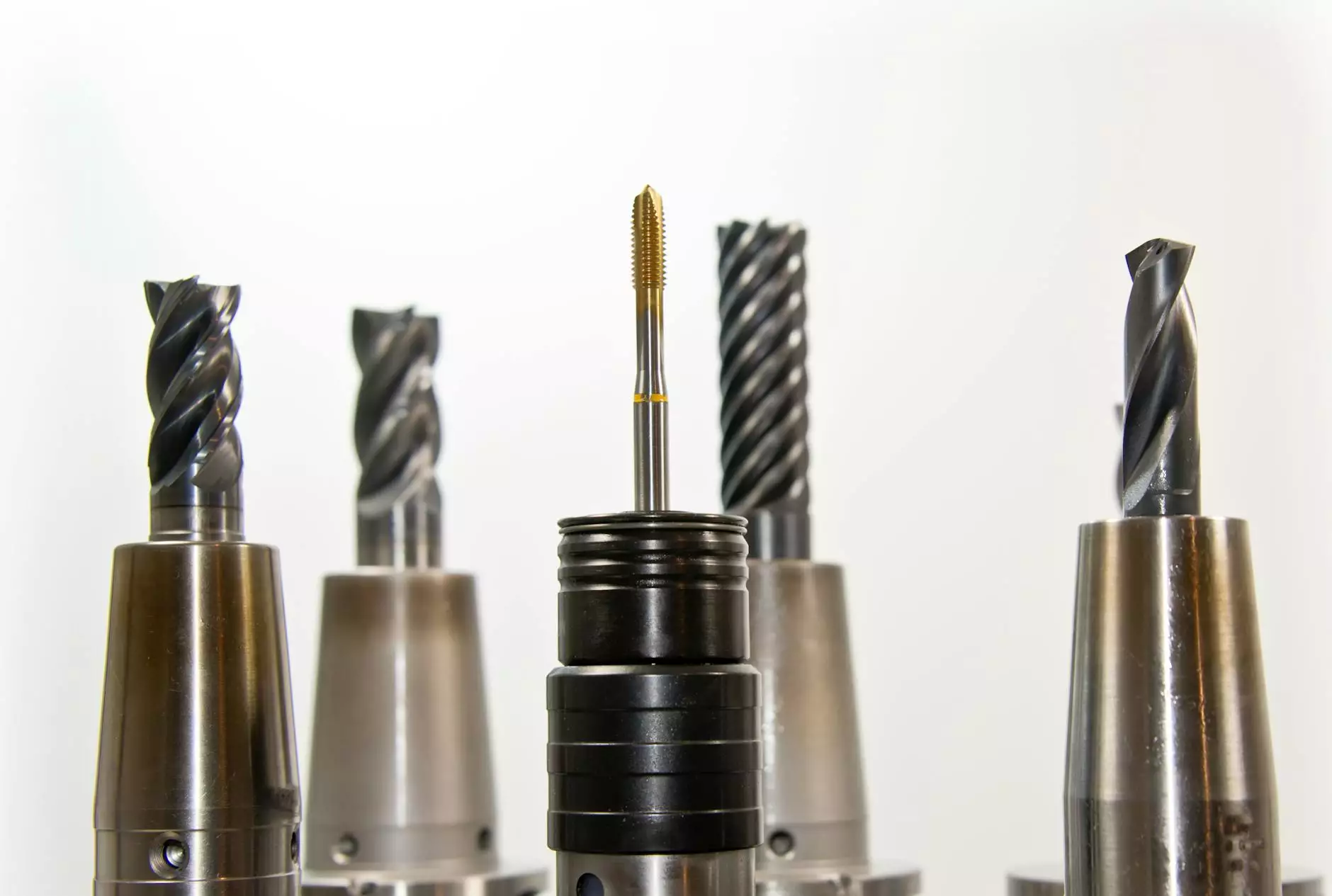
Precision machining CNC refers to the advanced manufacturing process that uses computer numerical control (CNC) technology to produce highly accurate and consistent metal parts. With the increasing demand for precision in various industries, this technique has emerged as a cornerstone of modern manufacturing. In this article, we will delve into the intricacies of precision machining CNC, its applications, benefits, and the pivotal role it plays in industrial metal fabrication.
What is Precision Machining CNC?
Precision machining is a manufacturing process that utilizes the precise movements of CNC machines to cut and shape materials, usually metals, into desired dimensions with acute accuracy. The term "CNC" stands for Computer Numerical Control, which signifies that the machinery is operated through coded instructions that dictate its movements with exacting precision.
The Mechanics of CNC Machining
At the heart of precision machining CNC lies the CNC machine itself, which is programmed using CAD (Computer-Aided Design) designs to create complex components with intricate details. The process involves:
- Designing: Engineers create detailed models of the component using CAD software.
- Programming: The CAD model is translated into a CNC-programmable format.
- Machining: CNC machines precisely cut or mill the materials following the programmed instructions.
Key Benefits of Precision Machining CNC
The efficient capability of precision machining CNC comes with multiple benefits that make it indispensable for industries:
1. Enhanced Accuracy
One of the most notable advantages of CNC machining is its ability to produce parts with high levels of accuracy. Components can be manufactured to tolerances as tight as ±0.001 inches, making them suitable for industries where precision is critical, such as aerospace and medical manufacturing.
2. Consistency and Reproducibility
Following the same CNC code ensures that every part produced is identical. This level of consistency is essential for industries requiring mass production, where uniformity must be preserved across each component.
3. Efficiency and Speed
The automation of the machining process means that CNC machines can operate continuously, producing components at a much faster rate than manual machining, thereby increasing overall production efficiency.
4. Complex Design Capabilities
CNC machining can easily create parts with intricate geometries that would be difficult, if not impossible, to create with traditional machining techniques, expanding the possibilities for design and creativity in product development.
5. Cost-Effectiveness in the Long Run
While the initial investment in CNC equipment may be high, the long-term savings accrued from reduced labor costs and minimized material waste often outweigh this initial outlay.
Applications of Precision Machining CNC
The applications of precision machining CNC are vast and varied, stretching across multiple industries:
Aerospace Industry
In aerospace, components must withstand extreme conditions and be manufactured with utmost precision. CNC machining meets these rigorous standards, making it an essential process in the production of aircraft parts.
Medical Sector
The medical industry relies on precision machining for producing surgical instruments, implants, and devices that require exact specifications to function properly and safely.
Automotive Manufacturing
The automotive sector benefits from CNC machining in creating engine components, gears, and other parts that must maintain exact tolerances to ensure performance and safety.
Electronics
CNC machining is used to manufacture electronic housings and components, which often have strict dimensional requirements due to the compact nature of modern electronics.
Choosing the Right CNC Machining Partner
When selecting a precision machining CNC partner, consider the following factors to ensure you collaborate with a reputable provider:
- Experience: Look for companies with a proven track record in the industry, such as Deep Mould, known for its expertise in metal fabrication.
- Technology: Choose a provider that utilizes the latest CNC technology, which can significantly enhance production capabilities and lead times.
- Quality Assurance: Ensure the company has robust quality control processes that guarantee the accuracy and reliability of its produced components.
- Customer Support: A good machining partner will offer excellent customer service and support for any queries or concerns you may have throughout the process.
Future Trends in Precision Machining CNC
The landscape of precision machining CNC is ever-evolving, with several trends likely to shape its future:
1. Integration of AI and Machine Learning
The incorporation of artificial intelligence into CNC machining systems could enhance operational efficiency by enabling predictive maintenance and optimizing machining parameters based on real-time feed data.
2. Increased Automation
With the rise of Industry 4.0, more manufacturers are adopting automation technologies to streamline processes, allowing CNC machines to communicate with other operational systems seamlessly.
3. Use of Advanced Materials
As industries demand more durable and lightweight materials, CNC machining will evolve to work effectively with advanced alloys and composites, expanding its application scope.
4. Sustainability Practices
Increasing attention towards environmental sustainability will lead to innovations in CNC machining, focusing on reducing waste and energy consumption throughout the manufacturing process.
Conclusion
In conclusion, precision machining CNC is a transformative process that has brought significant advancements to metal fabrication and manufacturing. Businesses like Deep Mould exemplify how precision machining can be leveraged for exceptional product quality and efficiency in various industries. As technology continues to advance, the possibilities within precision machining will expand, shaping the future of manufacturing and enhancing economic growth.
Investing in precision machining capabilities is not just a game-changer for product quality but also a strategic move towards long-term sustainability and success in an increasingly competitive industrial landscape.